Lean process improvement is a business methodology that helps companies eliminate waste activities from project operations while hyper-focusing on delivering value to customers. The main goal of lean process improvement is to enable project teams to identify and address opportunities to continuously improve upon process workflows.
Project teams that practice lean process improvement often use Kanban, Six Sigma, and other project management tools to manage lean process improvement initiatives. These techniques are most successful when implemented across an entire organization with stakeholder buy-in.
Lean process improvement has a direct impact on the revenue a company accrues. The more customers value the products or services a business has to offer, the more they are willing to pay. In addition to helping companies increase the value they can offer customers, lean process improvement optimizes workflows and reduces waste, enabling organizations like yours to effectively boost employee productivity and morale.
What is lean process improvement and why is it important?
Lean process improvement leverages a series of steps that help create a high level of efficiency within each department of an organization. More specifically, in order to facilitate implementation of lean process improvement, project managers and teams utilize lean process improvement tools and techniques. Lean process improvement techniques
Lean process improvement strategies leverage a number of potential problem-solving frameworks. These techniques help guide the execution of key lean process improvement steps.
Here are a few of the most popular lean process improvement methodologies that help project teams optimize their operations:
Kanban. Kanban is a Japanese project management technique that helps project teams visualize the workflows currently in place within their organization. The Kanban system utilizes Kanban cards as a visual representation of activities within a company process. This system enables project teams to minimize miscommunication and quickly identify constraints within operations.
Lean Six Sigma. Lean Six Sigma is a project management technique that relies on team collaboration to improve performance. This technique combines the focuses of lean methodology and Six Sigma, shifting the company focus to removing waste activities and reducing variation in operational workflows. Lean Six Sigma utilizes the define, measure, analyze, improve, and control (DMAIC) cycle to optimize business processes.
Total Quality Management (TQM). This customer-focused approach to process improvement involves continuous improvement over time. TQM relies on data-driven decision making and performance metrics to improve current business processes. TQM asserts that customers should determine the quality level of products and services. In TQM, operational performance is measured using data analytics and improvements are made based on the history (successes and failures) of previous operational workflows.
Lean process improvement tools
No matter which project management technique your organization chooses to facilitate process improvement, you will also need to make use of key process improvement tools. Lean process improvement tools such as value stream maps and process maps can help your team visualize opportunities for process improvement with existing operational processes.
Value stream maps. Value stream maps help lean teams focus on optimizing their value stream. In lean process improvement, the value stream is defined as all of the actions (both value-creating and non-value creating) that bring a product or service from concept to delivery.
Value stream maps resemble a high complex flowchart with multiple inputs. First, project teams must create a current state map that captures the current condition of a value stream’s material and information flow.
Next, the project team draws a future state map that depicts how materials and information should flow. This tool proves useful when analyzing current processes and identifying opportunities to improve existing processes.
Process maps. Process maps can offer businesses insight into the roles, responsibilities, and timelines of a particular business process. Project teams can use process maps to comb through the fine details of these processes and identify areas for improvement.
Process maps come in various forms including flowcharts, deployment maps, swim lane diagrams, and more. Lean process maps often focus on reducing the eight types of waste in operations to optimize workflows and aid continuous improvement. Here is an example of a lean process map built using MindManager.
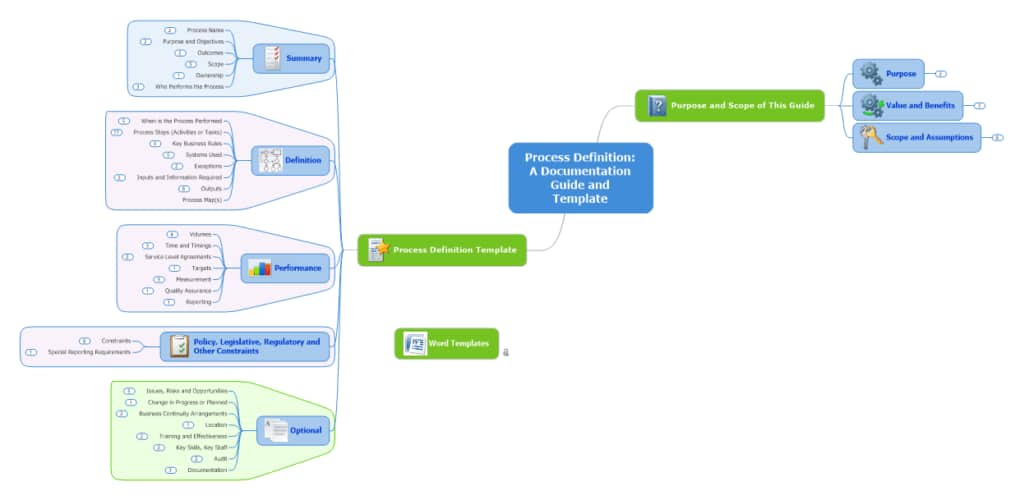
Create a process map using MindManager to aid lean process improvement initiatives.
The 5 main steps of lean process improvement
Once you have identified the project management techniques and tools that will help your team facilitate lean process improvement, you can begin implementing lean process improvement procedures.
Here are the five main steps of lean process improvement:
Identify and analyze which processes need improvement. It’s crucial for organizations to fully understand their current processes if they intend to make process improvements. Conducting a gap analysis or utilizing AS-IS mapping can help companies better understand what could be causing project delays or bottlenecks. An AS-IS map is a type of process map, typically a flowchart, that outlines the current state of a process so that teams can identify and implement improvements in the future.
Identify the improvements that should be made. After analyzing the workflow, project teams should begin to identify the process improvements that need to be made. Project teams should also model how these improvements can be implemented and conduct a risk analysis to address any quality or compliance issues that may occur during the implementation phase.
Implement process improvement tools and techniques. After modeling how the process improvement initiative will be implemented using techniques, project teams can begin to solicit stakeholder buy-in. Once the entire organization is aware of the change to come, project teams can begin to utilize process improvement techniques and tools to optimize current workflows.
Monitor process improvement execution. Once process improvement initiatives have been implemented, project teams should carefully monitor them for additional issues. Monitor your process improvement initiative by soliciting feedback from employees that are ingrained in the workflow that is being monitored. Keep in mind that change in process may uncover additional bottlenecks that must be addressed through additional process improvement cycles.
Assess the value of process improvement efforts. A large aspect of lean process improvement is the concept of continuous improvement, which seeks to continuously improve upon company processes to help with adaptability.
At the end of process improvement initiatives, project teams should ensure that each activity within a workflow is directly related to the value a product or service brings to customers. If the recent improvement initiative seems to provide little value to customer needs, it should be immediately reworked or eliminated.
How MindManager can improve your lean processes
Workflow visualization is a key part of lean process improvement because it enables companies to break down their operations into smaller parts and delineate which tasks should be eliminated to aid process improvement.
MindManager is a mind mapping software solution that helps businesses better visualize their company operations. MindManager includes several process mapping templates that can be used by organizations to enhance their understanding of existing company workflows.
With MindManager, project teams can enhance their collaborative efforts and overall team productivity by collaborating on mind maps simultaneously. MindManager aids project team collaboration by enabling users to save workflow templates for future use, saving teams valuable time and energy.